Recientemente estuve haciendo algunos cambios extra en el diseño. Por ejemplo, combiné en ambos diseños la tecla SHIFT corta + tecla de «menor y mayor» de las distribuciones ISO, junto con la tecla SHIFT larga de las distribuciones ANSI. Esto permite combinar distribuciones, algo que puede ser interesante para aquellos que prefieran la tecla de RETURN americana, pero quieran usar una distribución española, por ejemplo.
También aproveché para añadir dos NeoPixeles más en los dos huecos que había entre F4 y F5, y F8 y F9, lo que permite aumentar las posibilidades.
Por supuesto, llegó también el momento de diseñar la carcasa, para lo que decidí aprovechar los resultados de un cursillo de diseño e impresión 3D que hice hace tiempo (¡¡¡¡Gracias por convencerme para ir, Miguel!!!!). No tendría que ser demasiado difícil…
El primer problema que me encontré fue que el teclado mide 32cm de ancho, pero las impresoras 3D normales tienen una cama de entre 20 y 30cm, lo que significa que no podía imprimirlo todo de una sola vez sino que tendría que dividir la carcasa en dos mitades que se pudiesen pegar. Ante esto comencé con el primer diseño:
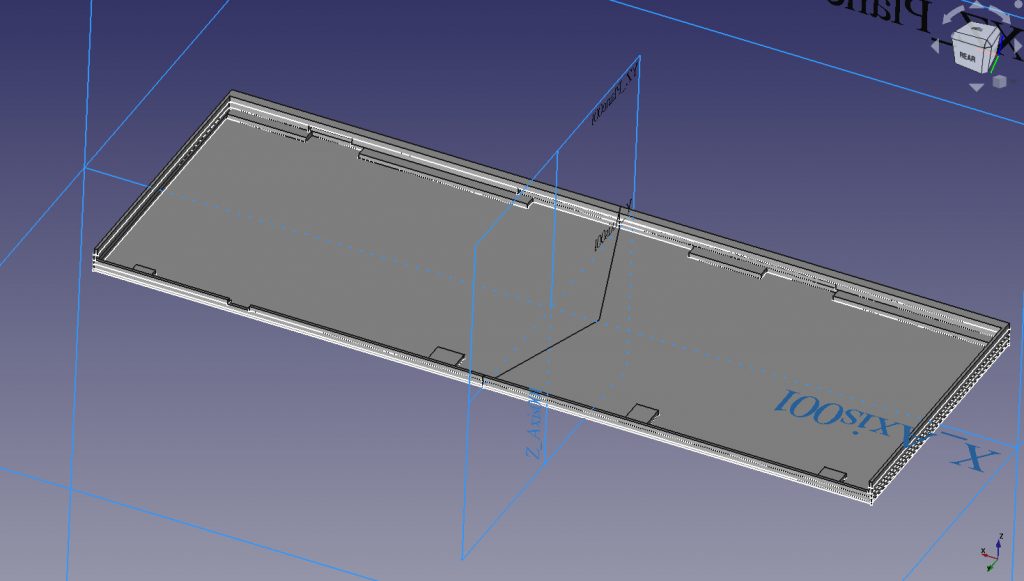
Como base no estaba mal, pero faltaban las patas y cubrir los huecos entre las teclas. Para ello se me ocurrió que podía utilizar una pieza que se añadiese por detrás.
Menos mal que se me ocurrió probar a imprimirla antes… ¡Menudo desastre! Se suponía que la parte delantera, que es la que queda hacia el fondo en la imagen, tenía unos huecos en donde la placa se introducía para quedar fijada; por desgracia, para imprimirlos hacía falta utilizar soportes, los cuales no había manera de quitar en una zona tan estrecha como una placa de circuito impreso. Ante esto, decidí probar un segundo diseño:
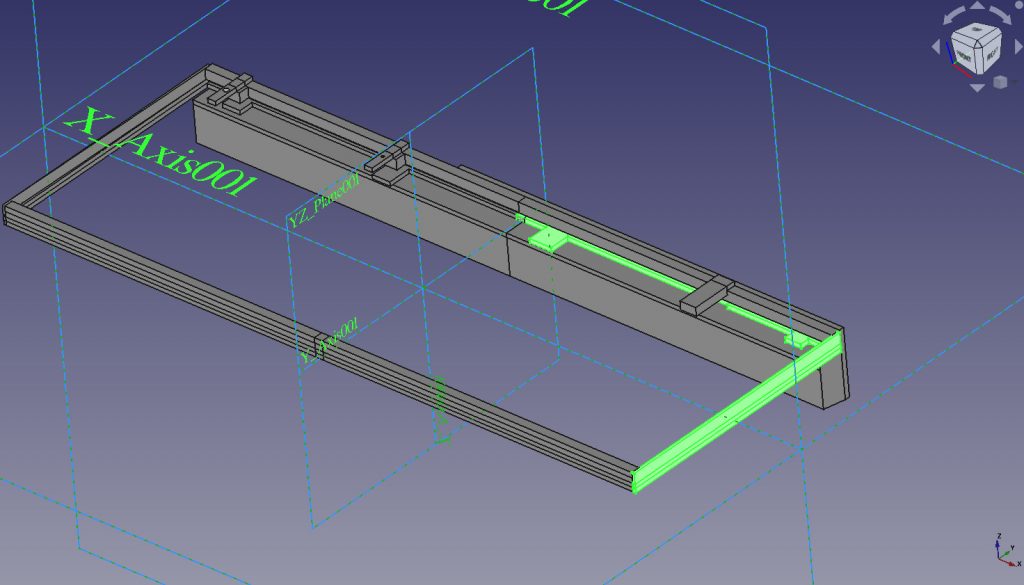
En este nuevo diseño, el bloque principal de la carcasa estaba compuesto por cuatro piezas en lugar de dos (a mayores hay dos piezas extra para hacer una pata que va de un extremo a otro). Las dos piezas traseras se imprimirían «planas», pero las delanteras, en donde estaba la ranura en donde encajaría la PCB, se imprimiría «hacia arriba», con el frontal apoyado en la cama. De esta manera se podían evitar los soportes.
Por desgracia, aún era demasiado complicado, pues la parte de la pata consumía muchísimo filamento y no era nada sencilla de montar. Además, la alineación de las cubiertas para las zonas entre las teclas era crítica, pues hay menos de un milímetro de margen: un error, por pequeño que sea, haría que las teclas rozasen o, peor aún, no pudiesen bajar… como de hecho me ocurrió.
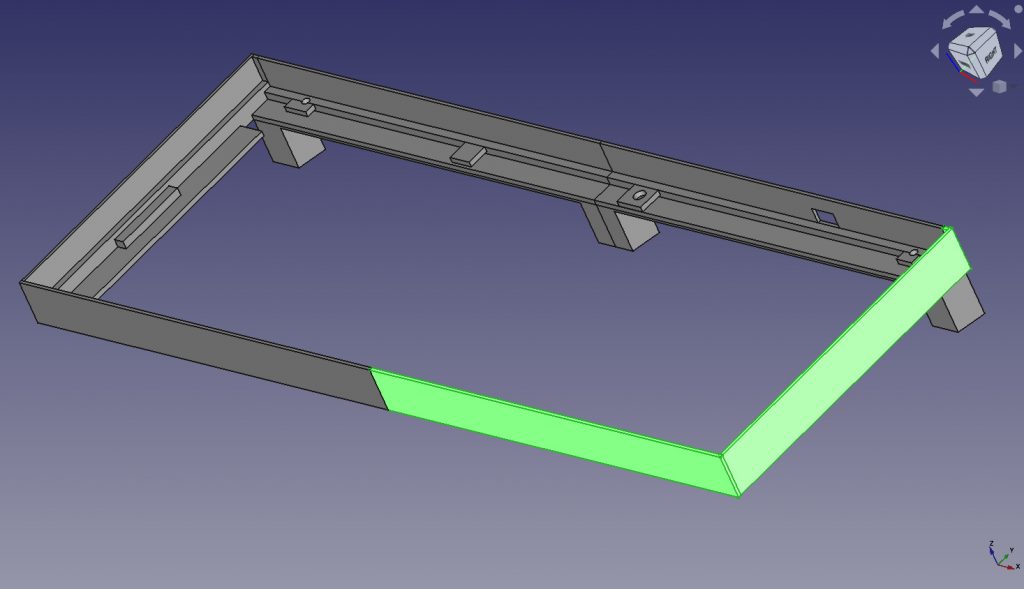
Finalmente, tras darle muchas vueltas se me ocurrió que podía simplificarlo muchísimo si separaba las cubiertas de los huecos de la carcasa, de manera que fuesen piezas independientes. De aquí salió el diseño de arriba: las dos piezas traseras se imprimen rotadas 90 grados, mientras que las dos piezas delanteras se imprimen «tal cual», de manera que no hace falta ningún tipo de soporte. El diseño lo hice sin la base para ahorrar plástico, pues quería usar un trozo de lámina de polietileno recortada para abaratar costes y reducir el tiempo de impresión.
Las piezas para cubrir los huecos entre las teclas de función las imprimí aparte, con la intención de pegarlas directamente en la PCB. Esto no sólo simplificaba mucho el diseño, pues no había que hacer malabares para evitar tener que usar soportes, sino que, además, eliminaba completamente los problemas de falta de precisión:
El diseño tenía buena pinta, pero aún no me acababa de convencer, pues había que pegar cuatro piezas para construir la carcasa, lo que no era muy cómodo. Además, la idea de ahorrar costes utilizando una lámina de polietileno como base no resultó: para empezar, las ranuras que había en el diseño para que ésta encajase eran demasiado estrechas, algo que, además, dependería de la impresora en sí. Pero además, si quería que las piezas se imprimiesen bien, no me quedaba más remedio que imprimir una «balsa», con lo que el ahorro no era tal, pues al final estaba imprimiendo la base igual, sólo que la tiraba a la basura.
Finalmente, llegué al diseño actual, que es éste:
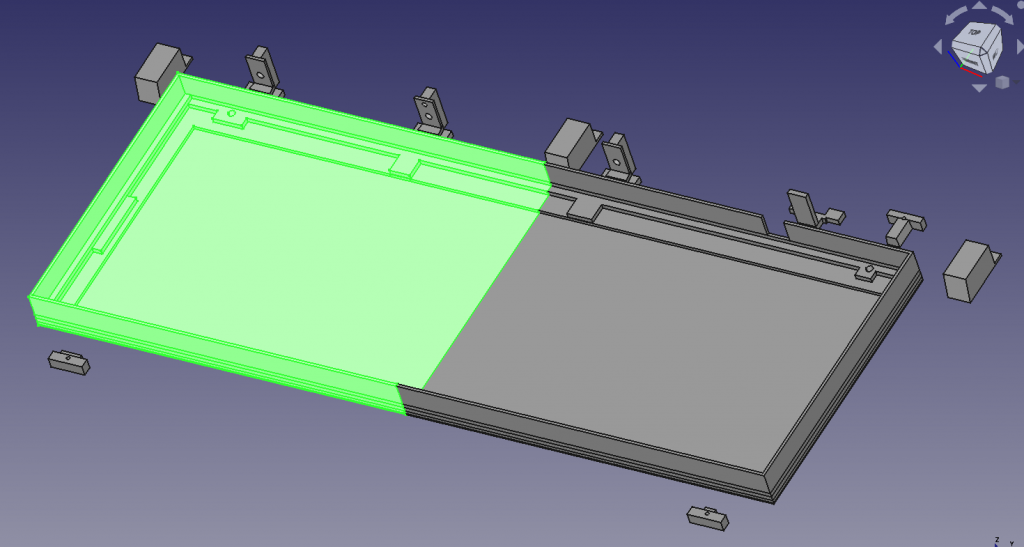
La carcasa en sí está compuesta por solo dos piezas, las cuales, además, son muy fáciles de pegar. La superficie principal de la base tiene un grosor de sólo 0,6 milímetros, lo que significa que se gasta la misma cantidad de filamento que si se utilizase una «balsa» con el diseño anterior; sin embargo, la resistencia es la misma, pues en los bordes el grosor aumenta para darle rigidez. Las patas se imprimen aparte y se pegan en el borde trasero. Esto tiene la ventaja de que es posible imprimir patas de distinta altura para ajustarlo a las preferencias de cada uno. Por último, las cubiertas se imprimen aparte, como se ve, y además hay tres piezas extra que también se pegan entre las teclas y que sirven como «tuercas» para atornillar la placa a la carcasa (aunque en los dos teclados que hice no fue necesario, pues quedaron perfectamente ajustadas).
Y el resultado final es éste:
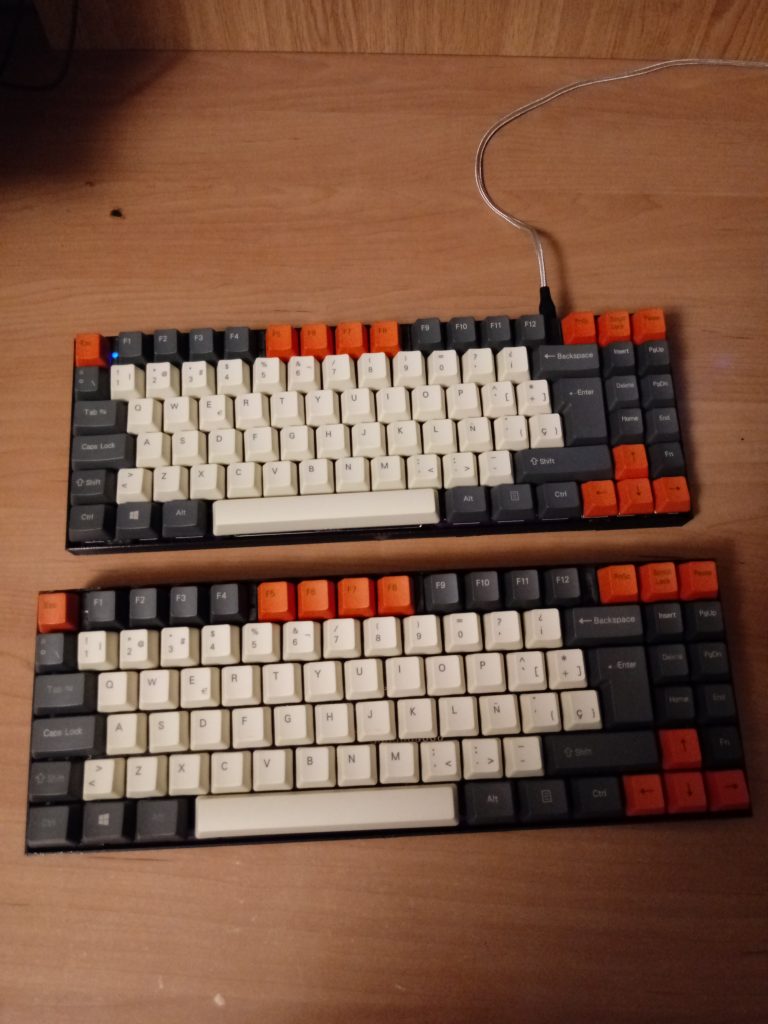
Problemas tecladiles (5) por A cuadros está licenciado bajo una Licencia Creative Commons Atribución-CompartirIgual 4.0 Internacional.